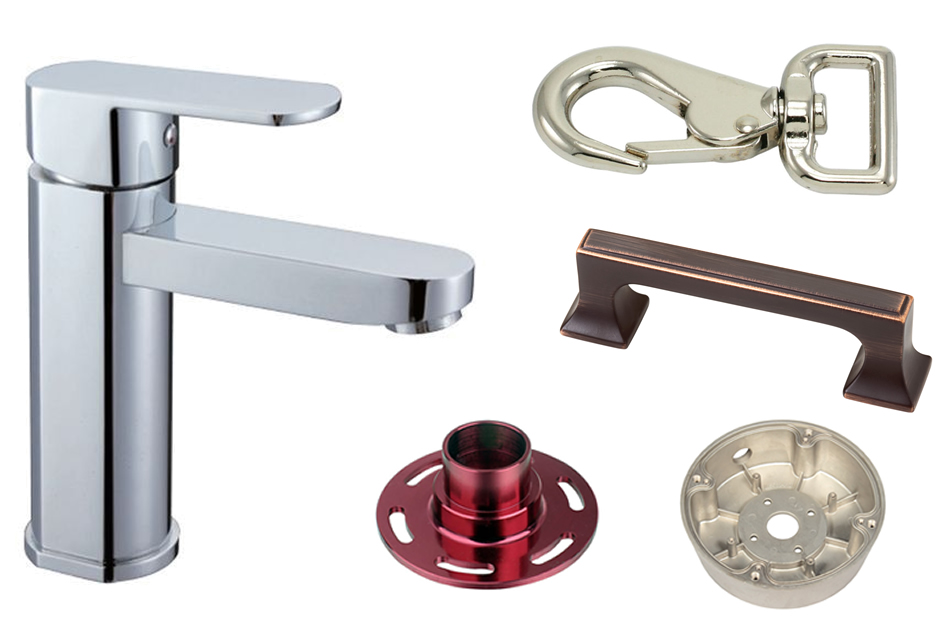
Precision Zinc Casting
High strength and hardness make die cast zinc the ideal alternative to machined, pressed, stamped, and fabricated items. Zinc’s strength and durability, combined with its finishing options makes it a top choice for many consumer goods.
There are two basic zinc casting alloys: ZAMAK alloys and ZA alloys. The majority of zinc castings are made with Zamak alloys, which contain approximately 4% aluminum and provide zinc castings with excellent strength. ZA alloys contain higher amounts of aluminum and offer superior strength.
Zinc casting alloys are stronger than reinforced molded polymers. Zinc’s hardness, self-lubricating properties, dimensional stability and high modulus make it suitable for working mechanical parts, such as gears and pinions.
Zinc’s excellent thermal and electrical conductivity, as well as precise casting tolerances, make it an ideal material choice for heat sinks, electrical components and applications requiring electromagnetic shielding.
Advantages of Zinc Die Casting
- Low Cost Raw Material
- Casting Process Flexibility
- Long Tool Life
- Fully Recyclable
- High Precision | Close tolerances
- Excellent thin wall Capability
- High Dimensional Accuracy & Stability
- Superior Strength | Impact Resistant
- Excellent Corrosion Resistant
- Thermal & Electrical Conductivity
- High Quality Finish
- Easily to Anodize, Paint, or Plate
- Moderate casting temperatures provide significant energy & processing savings